Formability of Powder Metallurgical Al-Ti Components under Compression
Formability of Powder Metallurgical Al-Ti Components under Compression
Dr. Tharmaraj Ramakrishnan
Assistant Professor in Mechanical Engineering, SRM Institute of Science and Technology (India)
Brief Biography: Dr. Tharmaraj Ramakrishnan is an accomplished mechanical engineering academic and researcher with a Ph.D. from National Institute of Technology Warangal, India, and a Postdoctoral Fellowship from the Polish Academy of Sciences. With over six years of teaching experience and strong research credentials, he currently serves as an Assistant Professor at SRM Institute of Science and Technology, Chennai. His expertise includes powder metal forming, additive manufacturing, dissimilar material joining, and simulation of manufacturing processes. He has authored 19 international journal papers, 14 international conference papers, and contributed to books published by CRC Press. He holds one patent and has received national research funding under the DST-INSPIRE scheme of Indian Government. Dr. Tharmaraj is actively involved in organizing conferences, faculty development programs, and expert talks. He serves as a reviewer for leading journals and holds memberships in professional bodies. His academic excellence is recognized by multiple awards, including gold medals and best paper presentation honors. He has mentored undergraduate projects and participated in numerous faculty development and training programs. His contributions to mechanical engineering education and research, particularly in composite materials and joining technologies, demonstrate a strong commitment to innovation and academic leadership.
Talk Abstract: In this talk, the formability behaviour of powder metallurgical aluminium-titanium components is discussed. This talk sheds light on research in which powder metallurgy process was used, the necessary specimens were created with varying initial relative densities (80–90%) and an aspect ratio of 1 by applying the proper compaction pressures. Using a hydraulic press, a series of upsetting procedures has been carried out on the powder metallurgical compacts with varying titanium compositions (2–6%). The accumulation of stresses and the presence of pores at the damage location are the primary causes of the specimens’ damage during compression. Therefore, using finite element simulation software, the damage location of the compacts was determined for different specimens. The compacts were heated to varying degrees at the damaged areas once the damaged position was determined.
Moderators: Prof. K Gupta and Mr. Olehile Kaelo, Mechanical and Industrial Engg. Technology (DFC)
Time: 10:00-11:00
Date: 08 July 2025
Disclaimer: The University of Johannesburg encourages academic debate and discussion that are conducted in a manner that upholds respectful interaction, safety of all involved, and freedom of association as enshrined in the law, the Constitution, and within the boundaries of the University policies. The views expressed during events are expressed in a personal capacity and do not necessarily reflect the views of the University of Johannesburg.
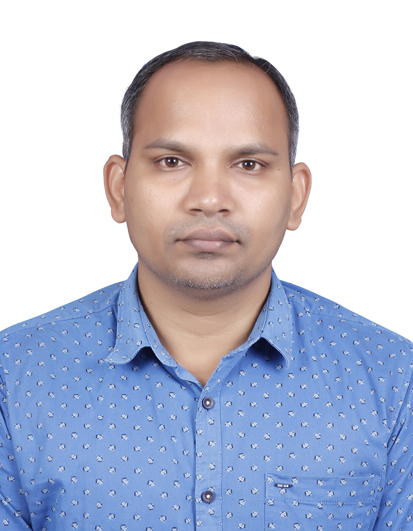